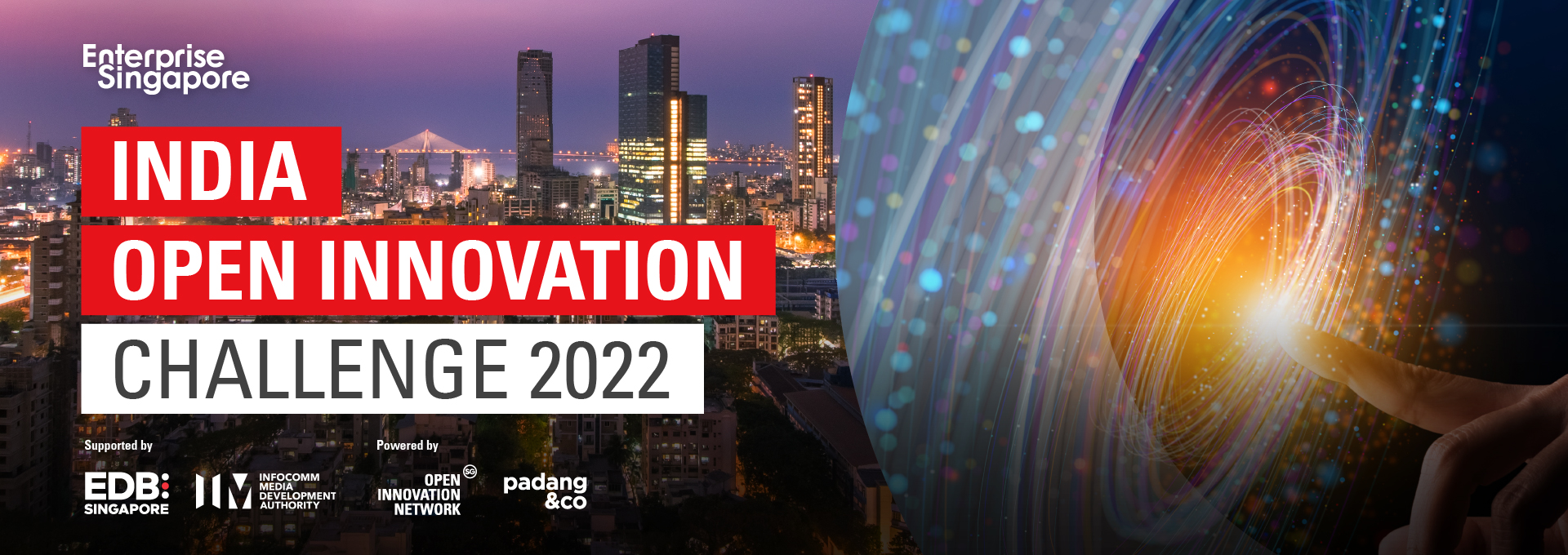
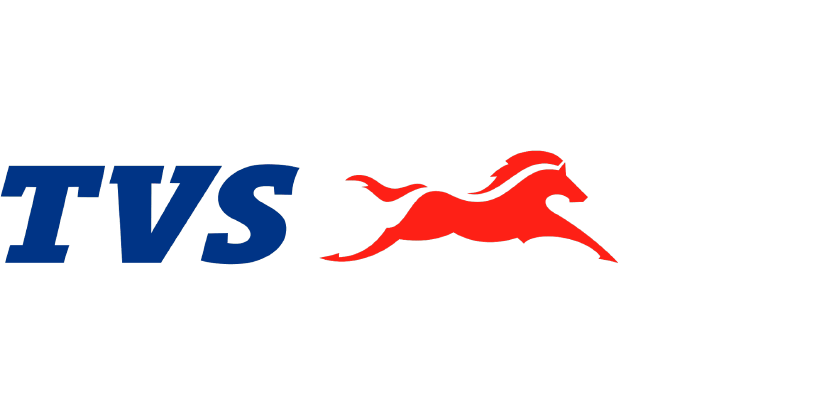
How might we set up a future ready manufacturing facility to achieve ZERO defect assembly lines with automated inspection using computer vision and Hand Motion Analysis (HMA)?
Background/Context
Operators perform tasks along with pre-programmed machines across assembly lines in a set of predefined sequences. Even though the current system has a well-established process, human errors still occur. In addition, the system lacks data, insights of real-time analytics of operator actions, and alerts for deviations in the process flow.
Visual inspection by operators varies from person to person, and thus could sometimes lead to a defective product.
Though computer vision has been in use in manufacturing for decades, recent advances in Machine Learning (ML) and image processing have enabled new use cases. No longer limited to structured, repetitive tasks. AI-assisted, high-level computer vision and Hand Motion Analysis solutions are capable of functioning in increasingly complex, high-speed manufacturing environments and in conjunction with operators.
The desired result is improved efficiency, fewer errors, and better data.
Objective
TVS believes that industrial transformation is an opportunity to elevate the manufacturing facility using AI and ML-based computer vision and Hand Motion Analysis (HMA) to monitor the actions of an operator in real-time, and enable defect-free assembly lines to unlock the potential for long-term competitiveness and sustainability.
Solutions
First, TVS would like to explore a solution for one of their engine assembly lines. The desired solution should fulfil the following requirements:
- The solution is ready for mass-production engine assembly and vehicle assembly lines with high-speed conveyors.
- It should have the intelligence to ensure whether the right part is picked for assembly by the operator.
- It may capture and analyse the hand movement of the operator using HMA technology to ensure adherence to a preset sequence and cycle time (time allocated for each station) for every part of the assembly.
- As current engine assembly lines have the capability to produce multiple models in the same engine line, the solution should have the intelligence to identify whether the operator picked the right part among different parts across various models. The operation is for only one model; it should not interfere with other variant production.
- The solution should be capable of connecting defects to the stage where it occurs and alerting the operator in real time.
Reward
- Successful company will conduct a pilot project with TVS spanning three months to validate the solution and go into a commercial deployment immediately after incorporating all the learnings from the pilot phase. After successful implementation in engine assembly of one plant, it can be extended to the other engine assemblies and vehicle assemblies of TVS Motors.
- The pilot project will be supported by a SGD20,000 grant from Enterprise Singapore and close guidance from the TVS Motors team.